Bauer : Le processus derrière un changement de vocation industrielle

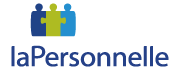
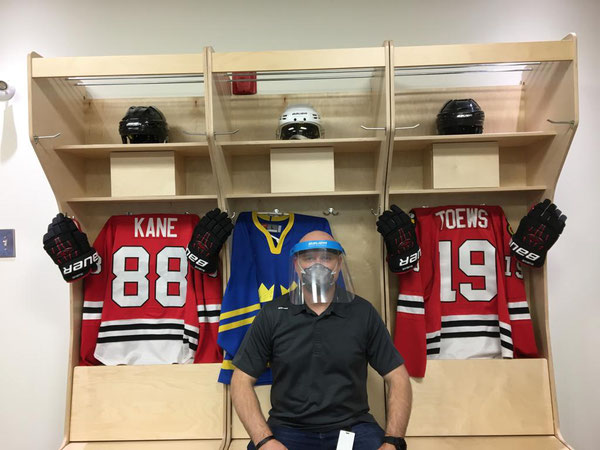
La crise actuelle nous destabilise et nous oblige à faire preuve de créativité et à innover. C'est le cas de la compagnie Bauer qui a récemment fait l’annonce de la modification de la chaîne de production de son centre d’Innovation de Blainville afin de produire des visières de protection pour le personnel soignant en première ligne dans la lutte au COVID-19. Cette annonce n’était en fait que la ligne d’arrivée d’un processus entamé quelques semaines auparavant.
L’une des personnes derrière cette réalisation, Thierry Krick ing., gestionnaire de l’ingénierie, développement de produits avancés et membre de Genium360, a accepté de nous éclairer quant aux étapes nécessaires à la mise en marché de leur nouveau produit.
Celui-ci se destinait au départ à l’architecture navale mais, après une première année d’étude, décida plutôt de s’orienter vers le génie mécanique étant attiré par la diversité de la discipline « le côté création, conception et fabrication d’objets et de systèmes. »
D’une idée à du concret
« Ce qui différencie la visière Bauer des autres est la forme de la mousse, plus épaisse au milieu afin de mieux épouser la forme du visage. » - Thierry Krick
« Tout a commencé un dimanche matin par un courriel, toute l’équipe de design s’est immédiatement réunie virtuellement pour voir ce que nous avions de disponible sur place », nous dit Thierry. Le centre de Blainville était déjà muni d’un grand centre de prototypage et d’usinage, lui permettant de faire des coulées, numériser puis imprimer en 3D et thermoformer des matériaux et des outils. De plus, l’équipe avait accès à des technologies développées à l’interne, dont la mousse Aerolite®, qu’ils voulaient initialement utiliser pour la visière.
Le lendemain, quatre idées en main, ils ont commencé à les tester ainsi qu’à rechercher les normes en vigueur. Une norme acceptée dans l’industrie concerne la distance qu’il doit y avoir entre la visière et le visage et qui est établie à 35mm, la leur en a 45mm « car on a voulu laisser plus d’espace pour les lunettes et les masques qui seront portés en dessous », précise Thierry. Lors du déploiement 3D de leur dessin, ils se sont aperçu qu’une mousse pleine courbée serait moins efficace pour la livraison et ont donc changé pour le modèle « en accordéon » pouvant se mettre à plat dans les boites.
Matériaux recherchés
Une fois le prototype final en main, l’étape suivante fût la recherche des matériaux nécessaires à l’industrialisation auprès de leurs fournisseurs réguliers. Certains d’entre eux provenant de l’international, les commandes furent un peu plus difficiles dans le contexte actuel. La visière est faite à partir de plastique PET sur lequel un film antibuée est appliqué. Devant le nombre de commandes grandissant de façon exponentielle, Bauer a trouvé en Cascades une planche de salut locale pour l’acquisition du PET et est actuellement à la recherche d’un fournisseur ou d’une technologie locale lui permettant d’ajouter le film antibuée. « Nous avons deux numéros de modèle en ce moment, l’un avec l’antibuée, dédié prioritairement aux hôpitaux, et l’autre sans » nous précise à nouveau Thierry.
Une ligne de production adaptée
« Avec les mesures de distanciation, nous avons dû revoir notre ligne de production pour nous assurer que chaque employé ait sa propre table et qu’elle soit située à 2 mètres de ses voisins. Ils doivent aussi suivre le protocole de salubrité mis en place et porter un équipement de protection complet. Chaque visière est assemblée en entier par la même personne plutôt qu’à la chaîne pour limiter les échanges. » - Thierry Krick
L’assemblage se fait en environ une minute par visière, entièrement à la main et utilise plusieurs pièces initialement dédiées à la production habituelle. « On essaie de descendre sous la minute et on devrait y arriver sous peu », nous dit fièrement Thierry. Une seule machine a dû être modifiée et une autre a trouvé une nouvelle utilité : « La machine à fil chaud sert maintenant à couper les élastiques plutôt que des sangles de casque et celle à œillets, à faire des trous », nous informe Thierry. Après quelques essais, un problème potentiel a été détecté dans la pose des rivets de l’élastique et une solution trouvée rapidement dans la réactivation d’un outil utilisé dans un projet antérieur. Ils l’ont numérisé et en ont imprimé des copies à partir de la machine de prototypage rapide. Une fois terminée, toute la production est envoyée dans un four où elle est chauffée à 60°C pendant une heure pour tuer toute trace potentielle de virus, soit le double du temps recommandé par un microbiologiste qu’ils ont contacté.
À situation urgente, réponse rapide de Bauer
« La philosophie chez Bauer est de tester nos produits longtemps avant de les mettre sur le marché pour nous assurer de leur qualité. » - Thierry Krick
La situation étant urgente, tout le processus s’est étalé sur seulement deux semaines et l’entreprise sera prête à livrer sa première commande cette semaine. Ils resteront donc à l’affût des commentaires de la clientèle afin de faire de l’amélioration continue. De plus, ils réfléchissent toujours à une façon de désinfecter les visières afin qu’elles puissent être réutilisées.
C’est donc ainsi qu’est née la première visière à vocation médicale de Bauer!
-
Déconfinement : des masques et de la soie
Audrey Bélanger O’Keefe, 12 mai -
La formation en ligne est-elle adaptée au génie?
Éloïse Martel-Thibault, 23 avril -
Jour de la terre : portrait de l’actualité sur l’impact environ…
Annie Passalacqua, 22 avril -
Quelles formations en ligne pour les ingénieurs?
Éloïse Martel-Thibault, 21 avril -
Entrevue
Être CPI dans une compagnie de service essentiel durant la pand…
Samuel Tremblay, 20 avril -
5 trucs pour être productif en télétravail
Éloïse Martel-Thibault, 16 avril -
Tout comprendre sur le PACME : formation subventionnée en temps…
Genium360, 15 avril -
Entrevue
Exercer son leadership en temps de crise : entretien avec Cloé …
Jean-François Thibault, 15 avril -
Se relever pour réussir : le parcours de Guillaume Parent
Jean-François Thibault, 09 avril -
COVID-19 : Mettons au défi nos ingénieurs québécois!
Jean-François Thibault, 06 avril -
Listes des mesures de soutien pour les entreprises, les travail…
Michel Landry, 02 avril -
L’ingénierie est une chevalerie
Jean-François Thibault, 23 mars -
Témoignages de la communauté du génie en temps de pandémie
Genium360, 19 mars -
Télétravail - Journal de bord d’une nouvelle réalité
Clémentine Alary Sery, 19 mars -
La gestion de projet à l’ère du COVID-19
Genium360, 18 mars